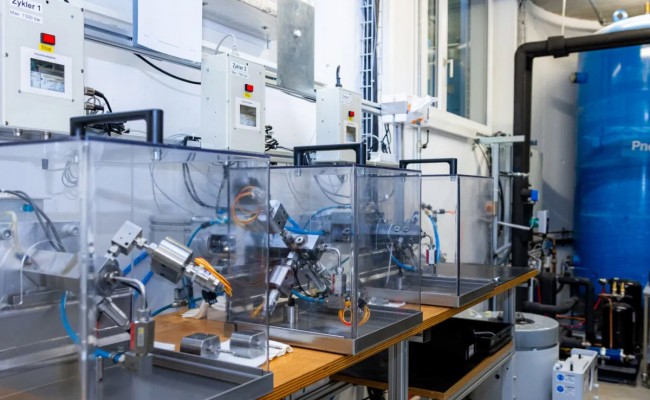
Keller: medidas aún más precisas
- 10/11/2024
Medir la presión es fácil si se puede utilizar un transmisor de presión. Pero, ¿cómo se puede convertir un buen sensor de presión en un transmisor de presión perfecto?
Nuestro director técnico, Bernhard Vetterli, nos ofrece una breve introducción sobre lo que se necesita para producir sistemas de medición precisos y fiables.
La información es la base de cada decisión y cada acción. Por eso, la medición, la inspección, la comparación y las pruebas son el punto de partida de todo tipo de medidas de optimización.
Sin datos no puede haber bucles de retroalimentación ni procesos de mejora. En el mundo de los sistemas de medición, estos desempeñan un papel decisivo. Es la única forma en que hemos podido perfeccionar nuestros productos a lo largo de las décadas.
Cuanto mejor conocemos nuestros productos, más oportunidades tenemos de desarrollarlos y optimizarlos y de aumentar la reproducibilidad de los resultados finales. La calidad de los productos depende del diseño y de los procesos de fabricación. La estrecha colaboración entre el equipo de diseño, los equipos de desarrollo de electrónica y software y el departamento de producción es un factor clave para el éxito de KELLER.
Sello de calidad para sensores KELLER: el original desde 1974
Electrónica
La compatibilidad electromagnética (EMC) exige que los manómetros resistan a la radiación electromagnética de hasta 6 GHz, a las descargas electrostáticas (ESD) y a las sobretensiones (caídas de rayos).
En KELLER, comprobamos otros factores que podrían causar problemas en aplicaciones prácticas reales. Por ejemplo, estamos optimizando nuestra nueva electrónica de sensores para garantizar que pueda funcionar cerca de inversores de corriente, vibraciones o fallos en la fuente de alimentación. Además, cada electrónica de sensores está equipada con un sistema que protege contra la sobretensión y la polaridad inversa.
Laboratorio de pruebas de compatibilidad electromagnética
Preparación para pruebas de vibración y choque.
Diseño mecánico
Los componentes de la carcasa, las costuras de soldadura, los diafragmas y las conexiones de presión se diseñan con la ayuda de herramientas de simulación (consulte el blog «Simulación FEM en el diseño» https://keller-druck.com/en/company/blog/fem-simulation-in-design). Esto nos permite reconocer y corregir posibles errores de diseño ya en la fase de diseño.
Pruebas de presión
Sometemos nuestros manómetros de alta presión a pruebas de presión de rotura y de presión de larga duración de hasta 4000 bares y no solo a temperatura ambiente, sino también en cámaras climáticas de hasta 200 °C.
Pruebas de presión de rotura y de presión a largo plazo en el laboratorio de pruebas mecánicas
Pruebas de larga duración
Nuestros sistemas de ciclos de presión funcionan las 24 horas del día y permiten picos de presión de hasta 1800 bares. Durante la fase de diseño, los productos se exponen a 10 millones de ciclos de presión entre el 0 y el 100 % del rango de presión especificado que garantizamos en nuestras hojas de datos. La curva de Wöhler, indica que ésto significa que se puede esperar resistencia para cualquier número de ciclos de presión.
Nuestros sistemas de ciclo de presión están en uso permanente.
Medición y pruebas en la producción
Los procesos de medición y prueba garantizan la calidad de nuestros productos. Pero también desempeñan un papel importante nuestros empleados altamente cualificados, que piensan por sí mismos, trabajan con atención y comprenden realmente los métodos y procesos. Los exhaustivos procedimientos de prueba en la producción y las mediciones que requieren mucho tiempo son, en última instancia, tan buenos como las personas que los llevan a cabo. Por eso damos mucha importancia a la precisión, la responsabilidad y el compromiso de cada empleado.
Pruebas intermedias en producción
Todos estos esfuerzos y mediciones se realizan y las desviaciones se caracterizan y corrigen para garantizar que nuestros clientes puedan confiar en resultados de medición precisos en todo momento. Les suministramos transmisores de presión con una señal de salida estandarizada y una banda de error total de ± 0,05 %FS en todo el rango de temperatura.
Las siguientes mediciones y pruebas se llevan a cabo durante el proceso de producción de sensores en KELLER.
Chips de sensores
El sensor de presión en sí es el corazón de nuestros sensores. Este consiste en un chip de silicio detrás de un diafragma de metal que convierte la presión física en una señal eléctrica. Antes de que se puedan instalar nuevos lotes de chips en producción, éstos se someten a un proceso de calificación de sensores supervisado por el departamento de desarrollo. Esto implica convertir los chips de sensores en celdas de medición y someterlos a pruebas exhaustivas. No se trata de un simple control de entrada de mercancías, sino que incluye no solo una medición completa del rendimiento a través de la presión y la temperatura, sino también una medición a largo plazo durante 3 meses a alta temperatura.
Oblea de silicio con aproximadamente 1200 chips sensores individuales
Mediciones a largo plazo de nuevos lotes de chips
Componentes mecánicos
En el proceso de montaje de los componentes mecánicos, todas las juntas se someten a pruebas de estanqueidad con helio. Esta prueba está integrada directamente en el sistema de estampación de los diafragmas metálicos ultrafinos del transductor de presión para garantizar que los componentes defectuosos no se sometan a un procesamiento posterior. Por supuesto, cada dispositivo de presión terminado también se somete a presión y temperatura para comprobar su resistencia a la presión y su integridad estructural.
Prueba de fugas de componentes mecánicos mediante helio
Características de cada sensor
Una vez que los chips de los sensores de presión se instalan en una carcasa con conexiones de presión y señal fácilmente ajustables, comienzan las mediciones de control y las evaluaciones iniciales, que pueden durar desde unas horas hasta varios días. La tecnología de sensores piezo-resistivos con su comportamiento característico en cuanto a temperatura nos ha llevado a instalar a lo largo de los años más de 60 sistemas de medición con un total de 12.000 estaciones de medición. A pesar de que los materiales y las máquinas de producción, así como la reproducibilidad de los procesos, mejoran constantemente, cada sensor de presión es ligeramente diferente y tiene sus propias características especiales. Por este motivo, KELLER prueba y evalúa en detalle el comportamiento de presión y temperatura de cada transductor de presión individual.
Instalación de los sensores en rieles adaptadores para pruebas de presión y temperatura en los sistemas de medición
Sistema de medición para medición de rendimiento a través de presión y temperatura.
Evaluación de los datos de medición
Compensación
Esta caracterización individual de los sensores permite una descripción matemática de la desviación del comportamiento ideal y una comprensión de cómo se puede compensar la desviación (véase el blog «Modelo de compensación matemática»). La información se puede poner a disposición del cliente en forma de coeficiente polinómico. En el caso de los transmisores de presión, los coeficientes se introducen directamente en el sistema eléctrico de compensación. Esta es la clave para lograr el «transmisor de presión perfecto» al que se hacía referencia al principio.
Modelado de las características físicas de un elemento sensor
Pruebas intermedias y finales
Una vez finalizados los importantes trabajos y antes de que los manómetros sean embalados y enviados, deben someterse a pruebas exhaustivas de funcionamiento y precisión en el llamado unitester. El unitesterha sido desarrollado internamente por KELLER con software y hardware específicos. Ha sido mejorado constantemente a lo largo de los años y puede ejecutar pruebas automatizadas.
Prueba final con el “unitéster” interno
Mediciones y pruebas posteriores
Los amplios trabajos de medición y pruebas que KELLER lleva a cabo en los sensores benefician directamente a los clientes con la caracterización individual y completa de los sensores.
Certificado de calibración con datos de medición de presión y temperatura.
La gran cantidad de datos de medición también proporciona a KELLER los datos estadísticos necesarios para comprender mejor las propiedades de los diferentes diseños de sensores y, por lo tanto, proporciona la base para mejorar continuamente los sensores.
Nuestro equipo de fabricación de equipos desarrolla soluciones de automatización que están hechas a medida de los requisitos de nuestro departamento de producción y que cumplen con nuestros altos estándares de calidad y precisión. Esto nos ha permitido mejorar continuamente nuestros productos, la estabilidad de los procesos y la eficiencia durante los últimos 50 años.
«El diseño, la implementación y la evaluación de pruebas como base para mantener altos estándares de calidad es un proceso altamente especializado con el que KELLER está profundamente comprometido.»
Bernhard Vetterli
Director técnico